3D printed heat exchangers at reduced costs and increased production volumes
A hybrid manufacturing process for thermal management devices that reduces development costs, increases production volumes and sustains quality.
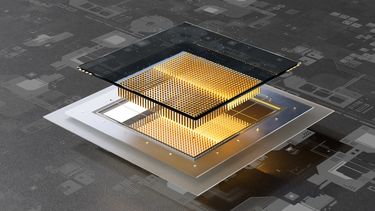
We are actively looking to engage with companies manufacturing or using additively manufactured heat exchangers, particularly those interested in testing our technology in-situ.
Background
Demand for bespoke heat management devices continues to increase as various industries search for advanced solutions to enhance thermal efficiency. By leveraging printing technology, industries can create highly efficient heat exchangers tailored to their needs, providing enhanced overall system performance with a focus on quality, repeatability and volume, at lower cost.
Metals remain the current mainstream answer for additively manufactured heat exchangers. Unfortunately, the process carries several drawbacks including complex software, parameter development, production, running and manufacturing costs, limiting true volume production and drastically restricting wider market opportunities. These drawbacks are compounded by extended product development cycles and high capital expenditure requirements.
Solution
Our solution employs a novel additive manufacturing design and plating methodology, employing advanced polymers and unique electroplating techniques. This innovative combination produces heat exchangers that are mechanically and thermally comparable to metal offerings, at a fraction of the cost. In doing so, it overcomes the drawbacks of additively manufactured metal offerings and encourages a transformative shift in high-performance heat exchanger production.
Benefits
- Aligned thermal performance to current metal additive manufacturing.
- Homogeneous smooth surface finish with no loose or partially sintered powder.
- Reduction in process complexity.
- Possibility to design thermally separate modes within a single manufactured part.
- Larger assemblies at reduced weight in various conductive materials.
- Suited to small or large applications such as medical, personal portable or industrial devices.
- Bespoke, low, or high-volume production at low cost.
- Opportunity to implement on existing and expanding market opportunities.