Developing longer-lasting saggars
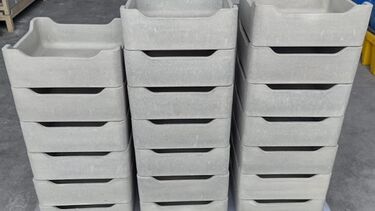
Reducing costs is the holy grail of battery production at scale – a philosophy that extends right through the supply chain, with any cost savings benefiting consumers. A collaboration between Morgan Advanced Materials and the University of Sheffield has helped Morgan develop a new, longer-lasting saggar – a ceramic box used in the production of cathode active materials – that could help manufacturers save money and avoid preventable accidents during manufacture.
What is a saggar?
Activating the precursor material used in battery cathode manufacture involves heating this material at an extremely high temperature in a tunnel kiln. Saggars are the ceramic boxes used to hold the precursor as it moves through the kiln, a process that can take up to 20 hours in an environment where temperatures routinely reach 800-900°C. These extreme conditions - and the corrosive nature of the precursor material - mean saggars have a limited shelf life.
“A saggar can typically withstand 30 cycles through the kiln before the risk of failure becomes too great,” says Inigo Anza, global technology director for molten metal systems at Morgan. “The precursor will start attacking the surface of the saggar and this leads to surface spalling and cracks appearing.”
If a saggar breaks in the kiln the consequences can be serious. The clean-up operation can take up to two weeks, costing manufacturers vital production time.
Testing times
Inigo’s team at UK-based Morgan develops and makes a wide range of refractories (materials resistant to heat) for different industries. It had been working on the new saggar for battery production, built using a proprietary material composition, at the suggestion of Richard Clark, Morgan’s former global lead for energy storage.
“Richard identified the need for this product, and knew we would need a lot of cathode powder to test it,” Inigo says. “He connected us with the team at Sheffield.”
At the time, the precursor powder used in the production of active cathode material was not easy to source in the amount required to prove the new Morganite LiB saggar longevity, due to it being a carefully guarded industrial secret by cathode manufacturers and not being commercially available. A team within the University of Sheffield’s Department of Materials Science and Engineering, then headed by Professor Serena Cussen (now at University College Dublin), was already producing its own precursors as part of the Faraday Institution FutureCat research project into next generation cathode materials. Morgan tasked this team with making larger quantities to test its saggar.
Narayan Simrit Kaur, now a Research Fellow at WMG, University of Warwick, was part of Sheffield’s team that produced the precursor powder for Morgan. She comments: “We were already making this powder in our lab, and part of our work was looking at how to scale up that process. Working with Morgan gave us the resources to do that.”
Inigo adds: “Sheffield provided us with two kilograms of the powder so we could do our internal qualification and testing. This was critical for us, without the powder we would not have been able to do the trial and error iteration and development that led to the finished product.”
Hitting the market
Morgan believes its finished saggar offers a 100% longer life compared to other products on the market. The company’s testing shows it can be used for up to 60 cycles for a typical coprecipitated polycrystalline NMC-811 powder, with less surface penetration by chemicals than other saggars. The saggar is also fully recyclable, and several companies have already shown an interest in using it in their production processes.
A demonstration line has been set up in India to make the saggars, and by the end of 2025 it will be capable of producing 10,000 units annually. But Morgan is thinking much bigger, and intends to set up a full production line in the US and Europe, with development kicking off as soon as the product takes off commercially. In a global ex-China basis, forecasts for 2026 estimate the consumption of around 1 million saggars a year. But as the battery industry matures this is expected to rise to 10 million a year by 2030, according to internal calculations and Volta’s most recent battery report.
All this would not have been possible without the support of the team at Sheffield. Though not a traditional research collaboration, Inigo says it shows the importance of strong links between industry and academia. Inigo commented, “Because we already working on so many different projects with Sheffield, we were able to leverage those relationships for this job.”
Professor Louis Piper of WMG, University of Warwick and Principal Investigator of the FutureCat project adds: “One of the legacies of the FutureCat project has been the strong industry engagement with transferring know-how and skills training to support the wider UK battery industry.”
By the numbers
20 - number of hours saggars can spend in the tunnel kiln as part of the cathode material production process
100% - increase in life cycle offered by Morgan’s saggar compared to other products on the market
10,000 - number of saggars due to be produced on Morgan’s demonstrator production line by the end of 2025
10 million - number of saggars expected to be required in the global ex-China battery industry by 2030