Research themes
Our world-class research is grouped into six different themes, enabling us to tackle the wider quality-of-life challenges in the 21st century.
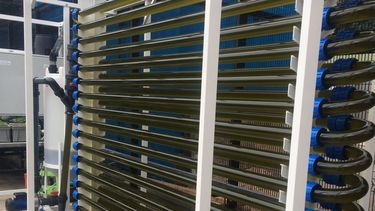
Energy and Sustainability
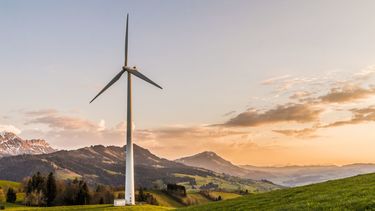
Environmental Engineering

Engineering for Health
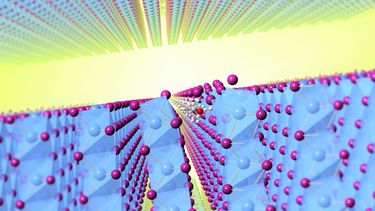
Multiscale Modelling and Optimisation
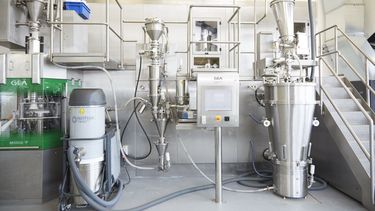
Processes and Manufacturing
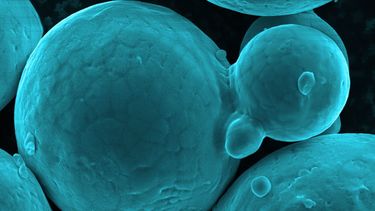
Materials Discovery & Characterisation