Design a gamma-titanium aluminide for additive layer manufacture
Gamma-titanium aluminides show great promise in high-temperature applications, their low density and high strength making them strong contenders for the manufacture of turbine blades, possibly supplanting the heavier nickel-based superalloys.
A range of alloy compositions is currently available, with compositions nominally similar to Ti-48Al-2Cr-2Nb that can be fabricated by additive layer manufacture (ALM) techniques. These techniques are related to the more familiar 3D printing technology.
In ALM, thin layers of alloy powder are laid down, and selected areas are melted layer by layer using high powered lasers or Electron Beam Melting. As more layers are added, a 3D structure is gradually formed, embedded in a block of alloy powder. The unused powder is mechanically removed at the end of the process, to reveal the final manufacture.
Current alloy formulations have been optimised for the traditional cast/wrought manufacturing route, and it was expected that improved formulations could be devised specifically for ALM using the techniques being developed by the DARE partnership. These techniques may increase our understanding of structure/property relationships for these alloys, and elucidate roles played by ‘impurities’, such as oxygen atoms.
Recent studies suggest that these may be key to pinning dislocations in this family of alloys, and so play a vital role in determining their properties.
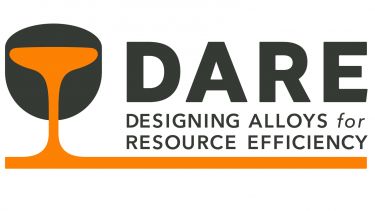
Designing Alloys for Resource Efficiency (DARE)
Addressing future resource challenges for alloys in manufacturing.