A chilling way to reduce train delays
Every year leaves on train lines cause delays to train services. Professor Roger Lewis and his team from Mechanical Engineering have developed a new cleaning technology that is on track to saving the rail industry millions.
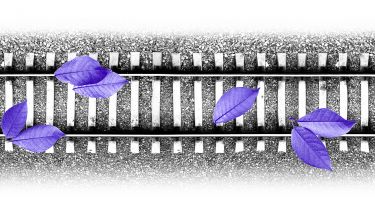
Every autumn, leaves fall onto railway lines costing the rail industry millions of pounds to remove. If not removed in time, they can cause delays and even accidents.
Professor Roger Lewis from the University’s Department of Mechanical Engineering led a team to develop an innovative leaf-busting cleaning system on trains in the North of England.
The team of researchers developed a system that uses dry ice pellets to freeze the leaves and blast them away from the railhead. Unlike current cleaning methods, this new, more sustainable device can be used on passenger trains allowing them to clean the tracks as they go.
Delays caused by leaves
There are around 10 million trees that line Britain’s railway. Every autumn, thousands of tonnes of leaves fall onto the wet railway tracks creating an effect similar to black ice on roads.
When the fallen leaves are crushed by trains, a slippery layer is created that generates traction problems. This causes wheels to lose grip and leads to problems with trains braking, and in extreme cases slipping along the rails. The risks caused by leaves on tracks mean that trains must run at a slower speed, accelerate less and brake earlier. A build-up of leaves can also make it harder for signallers to detect a train’s location causing further delays.
These issues cost the railway industry approximately £345 million each year.
The rail industry’s current solution to the leaf problem is by using specialised trains that deploy high-pressure water jets followed by the application of a gel containing sand grains and steel shot (Sandite). However, this only helps in the short-term as the Sandite does not always stick and a high percentage falls off the rail head.
Sheffield engineers have created a system that is significantly more efficient and can be used by passenger trains which cover more of the network than current fleets of cleaning trains. The system also doesn’t leave a residue, which can damage rails and train wheels, allowing it to be used on the same stretch of railway numerous times a day.
A chilling way to reduce train delays
Dry ice is frozen carbon dioxide with a surface temperature of -109.3 degrees. When put under pressure at low temperatures, carbon dioxide transforms from a gas into a solid but instead of melting like water, it returns to a gas form which is why it is often seen steaming or smoking when in contact with air.
As carbon dioxide is found naturally in the atmosphere and the dry ice used is re-claimed from other industrial processes, it has no negative effect on the environment. The carbon dioxide gas used to make the dry ice is a byproduct of producing fertiliser in the brewing industry and biomass powering stations, which further minimises waste involved. The properties of dry ice have made it adaptable to a range of industries. This includes preventing bacterial growth in the food industry, removing mould without chemicals in the cleaning industry and even storing organs for transplant in the medical industry.
Sheffield’s solution of using dry ice as a new rail cleaning technique involves blasting the dry ice pellets at super high speeds which breaks up the bond between the black leaf layer and the rail head. The contamination is removed through the action of the dry ice hitting the surface without leaving any residue or chemicals.
“The nozzle is aimed at the tracks and pushes air pellets out at a supersonic speed creating high kinetic energy. The pellets hit the surface at about minus 70 degrees and freeze the leaves. Within a fraction of a second, the pellet particles turn back into a gas and blast away any contamination on the tracks ” explains Professor Roger Lewis.
With funding from Innovate UK, early stage trials onboard trains were conducted in 2020/21 with Northern Railway and Tyne and Wear Metro operator, Nexus. Later in 2021, the University of Sheffield conducted further trials with Northern Railway to test the technology onboard an empty passenger train on the live rail network. The trials, which ran during autumn and winter 2021/2022 at speeds of up to 60mph, revealed the dry ice system is much more effective at removing leaves from the line, cleaning the track and reducing stopping distances than the methods currently used by rail industry.
Following the successful trials, the team are now modifying their system to fit underneath the carriage of passenger trains and giving a second lease of life to retired rolling stock as demonstrator units. The researchers have bought two retired Pacer trains, based at Wensleydale Railway, to test the new design and develop a plan for the system to be fitted on some Northern trains.
The system is expected to be installed and ready for testing on the live rail network in 2023, it will enable passenger services to clean the track when needed - particularly in months with more fallen leaves.
The dry ice cleaning system we’ve developed at the University of Sheffield has the potential to revolutionise how we clean the UK’s railways. Our trials over the last year have shown how it is a much better system for removing leaves from the line with train drivers reporting that it restores rails to almost new-like condition.
Professor Roger Lewis
Professor of Mechanical Engineering at the University of Sheffield and lead researcher on the project
“By installing the dry ice system on passenger trains it enables drivers to clean the track whenever they need it, to help avoid dangerous sliding events. It also means we can clean more of the UK’s rail network - reaching the branch lines served by local stopping services that so many people rely on. Wherever passenger trains go, the cleaning system could go - It could be used to clean every railway line in the country, if adopted widely” he adds.
Looking ahead
The continued success of the technology’s development in recent years has led to the creation of a new company - Cryo Technologies Limited. Through an agreement with the University of Sheffield, Cryo Technologies is transitioning the research into a commercial opportunity. Already available through Cryo Technologies is the “Cryogrip” modular road-to-rail system which has been used successfully for a whole Autumn season on the West Highland line in Scotland.
The team are also testing a new Machine Learning tool in Scotland in partnership with Network Rail and ScotRail that can predict friction levels on the line to turn the technology into a smart cleaning system. The tool was developed as part of a collaboration with the Rail Safety and Standards Board (RSSB) and the team is set to test the technology in Scotland in partnership with Network Rail and ScotRail.
The AI tool uses a camera and sensor fitted to the front and underneath of the train to predict friction levels on the track. This could act as an early-warning system for drivers - alerting them to upcoming sections of the track with low-adhesion and increased risk of sliding events, so they know when the dry ice cleaning system needs to be used and prevent further train delays.
“The cost of cleaning the UK’s rail network is huge, and even though our dry ice cleaning system uses reclaimed carbon dioxide and is much more sustainable than current cleaning methods, we still need to be considerate of how we use our resources when cleaning the line. By developing an AI tool that can predict friction, it enables us to optimise the system, so it’s cleaning the track when needed. The AI tool could transform our technology into a smart cleaning system, making it even more effective at reducing delays for passengers and saving money for the rail industry” says Professor Lewis.
Written by Alina Mironova, Marketing and Communications Officer (Research)