Using alkali-activated materials to develop sustainable construction materials
Researchers investigating how we can replace carbon-heavy traditional cement with cement made from alkali-activated materials, creating a sustainable alternative for a vital part of a city’s construction infrastructure.
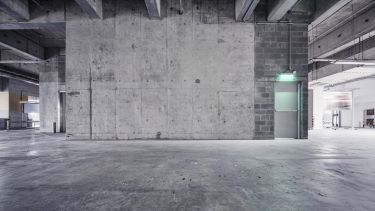
Currently, manufacturing cement is one of the most significant ways the construction of cities contributes to emissions. 0.8 tonnes of CO2 is produced per tonne of cement, and more than four billion tonnes of cement is used globally every year.
To continue to build cities and the buildings within them, the materials used to make cement and concrete must become more sustainable to produce.
Alkali-activated materials (AAMs) are an important part of the ‘future toolkit’ of sustainable construction materials. AAMs can be made using fly ash and slag, which are byproducts of power generation and steel production, via alkali activation. The result is a material that requires far less carbon than conventional Portland cement to produce. AAMs contribute to a circular economy through their use of waste from other processes, and can still provide the core functions of cement for our cities.
As well as reducing carbon emissions from cement manufacturing, AAMs are more resistant to the damaging effects of some common chemicals - problems which currently blight traditional Portland cement.
Cassandre Le Galliard, a PhD researcher from the Department of Materials Science and Engineering, is working on research into AAMs with Professor John Provis. The team is further developing understanding about both the product and the process of alkali-activation, linked to the European Marie Skłodowska-Curie ITN DuRSAAM with partners from Germany, Belgium, Croatia, Greece, the Netherlands, and Switzerland. Their research is intended to bring these new materials into large-scale use by understanding, modelling and predicting their durability in challenging service environments, which is also essential for the assessment of their life-cycle environmental footprint.
From this research, industry partners can gain information about the efficiency and performance of AAMs, which can encourage the uptake of a more sustainable material. So far, change in the industry has been slow. There are many elements to consider, including expenses, transportation, training and protection against the difficult-to-handle corrosive alkali solutions. Additionally, the conversion of traditional coal power plants to biomass fuel, and changes in steel production, has reduced the availability of the necessary fly ash and slag byproducts, which motivates work on finding alternative raw materials such as waste clays. Through research and testing, progress is being made in making the materials easier to work with, and showing that AAMs are an option for industry.
Our researchers are already working with the government and world organisations to highlight the potential of AAMs. Professor John Provis has significantly contributed to the British standard specification for sustainable AAM cements, and works with agencies including UN Environment to improve the uptake of sustainable cements.
Cassandre Le Galliard, who recently displayed her research at a public engagement event for the DuRSAAM ITN, explains: “Whilst AAMs are by no means a recent discovery - this type of cement has long been used in Russia and Ukraine - our research is driving forward the use of this low-carbon cement for construction more widely. Some industries, for example in Australia, are already using AAMs, and with further insight and ideas into the properties and benefits of the material, the process by which sustainable cement can be understood and utilised will become clearer and easier.”
Professor John Provis, Department of Materials Science and Engineering, said: “These cements are not expected to offer a like-for-like replacement of Portland cement across its full range of applications, for a complex range of reasons. However, when produced using locally-available raw materials, with well-formulated mix designs and production under adequate levels of quality control, alkali-activated binders are potentially an important and cost-effective component of the future toolkit of sustainable construction materials.”
Partner with us
To find out more about how you can work with our researchers please contact us on energyinstitute@sheffield.ac.uk